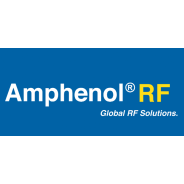
QA Supervisor (Fiber Optic Plant)
Công ty TNHH Amphenol Technology Việt Nam
Mức lương: Thỏa thuận
Kinh nghiệm: 3 năm
Nơi làm việc: Long An
Trình độ: Đại học
Mô tả công việc
1. BASIC FUNCTION
- Responsible for the Quality Assurance of the company.
- The QA Manager delegates the responsibility and authority to the Quality Assurance Engineer for ensuring the requirements of ISO 9001 are being observed and maintained.
- Company quality representative for all quality issues and ISO9001 and ISO14000 certification.
- In the absence of the AFOC Plant Manager, the Quality Assurance Manager will directly report to AFOP Director of Operations, and/or AFOP Director of Engineering and QA
2. SCOPE
- Responsible for overseeing continuous improvement and auditing of company processes with a concentration on ISO 9000, ISO 14001, TL 9000, and other Quality Management System, and the Corrective Action System. This position will interface at senior and executive levels with regard to ISO 9000, ISO 14001, TL 9000, and other Quality Management System process improvement and reengineering.
- All quality aspects of materials and products, purchased, manufactured and supplied by the company.
- Managing Equipment calibration and maintaining relevant documentation.
- Managing company ISO document
3. WORKPERFORMED
- Overall responsible for Quality at all AFOC facilities.
- Oversee, maintain, improve the company's ISO 9001:2000, ISO 14001, and other Quality Management program, Analyze and recommend appropriate changes of ISO procedures to respective managers.
- Verify that procedures are in use, functional and efficient.
- Assume the responsibility of Quality Management Representative for the company. Audit existing and new ISO procedures for compliance based on ISO or quality management program requirements and audit history.
- Coordinate and administer 3rd party quality audits, inclusive of schedules, communication, reports and tracking follow-up actions.
- Report ongoing activities to the AFOC Plant Manager, AFOP Director of Operation and Director of Global Engineering & QA and keep the company continuous improvement efforts on track.
- Assure Internal/External corrective action opportunities are channeled through the CPAR system, 8D report and/or other corrective form.
- Oversee and champion the Corrective Action system. Corrective Action system effectiveness.
- Oversee the corrective/preventive action program, inclusive of tracking status of open actions, receiving and reviewing responses, working with departments for timely completion and periodic reports.
- Monitor, evaluate and assign corrective actions to appropriate department heads for completion.
- Verify by auditing the effectiveness of corrective actions.
- Provide reports on problem to senior and executive management.
- ISO and Other Quality Management System process audits for all departments.
- RMA activity.
- Process Quality improvement functions.
- Supplier performance and inspection results; conduct supplier audits and formalize approval process.
- Collaborate with Engineering head to validate and verify all engineering projects’ outputs are complaint.
- Ensuring working closely with the Engineering head to ensure accurate and timely completion of all tasks related to the Engineering Project.
- Ensuring Working closely with the Operations/Production/HR on monthly reporting Service Level.
- Monthly Report Significant Events Related to Quality Department.
- Planning, directing and implementing policies and objectives of the department.
- Planning and manager company activities to ensure that RoSH, Reach, and Mineral Conflict are compliant with industrial and company policy.
- Directly interact with customers as necessary.
- Co-ordinate and implement specific TQM Programs to eliminate the incidence of defectives within acceptable "bench mark" limits.
- Monthly report per COP.
- Formulates personnel training programs on TQM.
- Ensures that manufactured products conform to established specifications of quality.
- Develops, controls and monitors budgets covering both internal and external quality services.
- Formulation and maintenance of Quality Policy and Procedures.
- Reviews routers and WIs, writes Quality Inspection Instructions for incoming materials and finished products, then, trains the QA inspectors.
- Administers system audit of the effectiveness of the Quality Policy and Procedures used in daily operations.
- Confers with management, technical representatives, suppliers and customers in the direction, planning and review of Quality Assurance, Quality Control and Certification.
- Additio
Yêu cầu công việc
- Equivalent Education Level Required
- Bachelor’s degree in engineering discipline or equivalent.
- Experience Required
- Minimum of 3 years experience in, or associated with, Quality functions.
- Knowledge Required
- Detailed knowledge and experience in Quality Control techniques and manufacturing processes namese & English.
Phúc lợi công việc
- Bảo hiểm theo quy định
- Du Lịch
- Thưởng
- Chăm sóc sức khỏe
- Đào tạo
- Chế độ nghỉ phép
Cách thức ứng tuyển
Ứng viên nộp hồ sơ trực tuyến bằng cách bấm nút Nộp đơn dưới đây
Nộp đơn 450 / 0
Từ khóa:
QA Supervisor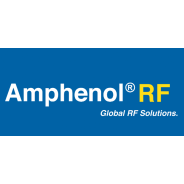
N1, Đường 1B, Khu xưởng Mở Rộng Kizuna 3, Khu K1, KCN Tân Ki,, Xã Tân Kim, Huyện Cần Giuộc, Long An
Quy mô: hơn 200 nhân viên

Trợ lý Pháp lý (Legal Assistant/ In-House Lawyer)
Công ty TNHH Yujin Kreves

Tuyển dụng Cố vấn Pháp chế
Chi nhánh Công ty Cổ phần Sản xuất - Xuất nhập khẩu Organic Herbs Group

Thực tập sinh ngành Luật
Văn phòng Thừa phát lại Long An

Cán bộ Pháp lý dự án (Kiêm giải phóng mặt bằng)
Công ty Cổ phần Phúc Long Vân

Nhân viên hành chính, tổng vụ
Công ty TNHH Kính Mắt Sun Yuan (Việt Nam)

Kế toán tổng hợp
Viện nghiên cứu và phát triển sản phẩm thiên nhiên (IRDOP)

Nhân Viên Phân Tích, Kiểm Nghiệm Viên Hóa Lý
Viện nghiên cứu và phát triển sản phẩm thiên nhiên (IRDOP)

Chuyên viên Pháp lý doanh nghiệp
Công ty CP Tập đoàn Lộc Trời

Tuyển dụng Nhân viên Pháp chế (Nam Từ Liêm, Hà Nội)
Viện nghiên cứu và phát triển sản phẩm thiên nhiên (IRDOP)

Trợ lý luật sư
Công ty Luật TNHH TA Law & Partners
Việc làm tương tự

Nhân viên Pháp lý (& CSKH Sau vay)
Công ty Tài Chính TNHH Một Thành Viên Bưu Điện

Nhân Viên Phân Tích, Kiểm Nghiệm Viên Hóa Lý
Viện nghiên cứu và phát triển sản phẩm thiên nhiên (IRDOP)

Nhân viên văn thư
Công ty Cổ Phần Bất Động Sản LEVACOM

Thực tập sinh Pháp chế
Công ty TNHH Dịch Vụ Lasun Hà Nội

Legal Executive
Công ty TNHH Giải trí đa phương tiện EPICMUSICVN (EMVN)
QA Supervisor (Fiber Optic Plant)
Công ty TNHH Amphenol Technology Việt Nam
Nộp đơn
Công ty TNHH Amphenol Technology Việt Nam